ਖੁਦਾਈ ਕਰਨ ਵਾਲੇ ਸਪੇਅਰ ਪਾਰਟਸ ਲਈ ਬਾਲਟੀ ਸਿਲੰਡਰ
ਐਪਲੀਕੇਸ਼ਨਾਂ
ਅਸੀਂ ਜ਼ਿਆਦਾਤਰ ਚੀਨੀ ਬ੍ਰਾਂਡ ਦੀ ਬਾਲਟੀ ਸਿਲੰਡਰ, ਐਕਸਸੀਐਮਜੀ ਐਕਸੈਵੇਟਰ ਬਾਲਟੀ ਸਿਲੰਡਰ, ਸ਼ਾਂਤੂਈ ਐਕਸੈਵੇਟਰ ਬਾਲਟੀ ਸਿਲੰਡਰ, ਕੋਮਾਤਸੂ ਖੁਦਾਈ ਬਾਲਟੀ ਸਿਲੰਡਰ, ਲਿਓਗੋਂਗ ਐਕਸੈਵੇਟਰ ਬਾਲਟੀ ਸਿਲੰਡਰ, ਡੂਸਨ ਐਕਸੈਵੇਟਰ ਬਕੇਟ ਸਿਲੰਡਰ, ਡੂਸਨ ਐਕਸੈਵੇਟਰ ਬਕੇਟ ਸਿਲੰਡਰ ਬਾਲਟੀ ਸਿਲੰਡਰ , ਲੋਕਿੰਗ ਐਕਸੈਵੇਟਰ ਬਾਲਟੀ ਸਿਲੰਡਰ, ਹੁੰਡਈ ਐਕਸੈਵੇਟਰ ਬਾਲਟੀ ਸਿਲੰਡਰ ਆਦਿ।
ਕਿਉਂਕਿ ਇੱਥੇ ਬਹੁਤ ਸਾਰੀਆਂ ਕਿਸਮਾਂ ਦੀਆਂ ਸਹਾਇਕ ਉਪਕਰਣ ਹਨ, ਅਸੀਂ ਉਹਨਾਂ ਸਾਰਿਆਂ ਨੂੰ ਵੈਬਸਾਈਟ 'ਤੇ ਪ੍ਰਦਰਸ਼ਿਤ ਨਹੀਂ ਕਰ ਸਕਦੇ ਹਾਂ। ਕਿਰਪਾ ਕਰਕੇ ਖਾਸ ਸਹਾਇਕ ਉਪਕਰਣਾਂ ਲਈ ਸਾਡੇ ਨਾਲ ਸੰਪਰਕ ਕਰਨ ਲਈ ਸੁਤੰਤਰ ਮਹਿਸੂਸ ਕਰੋ.
ਫਾਇਦਾ
1. ਅਸੀਂ ਤੁਹਾਡੇ ਲਈ ਅਸਲ ਅਤੇ ਬਾਅਦ ਵਾਲੇ ਉਤਪਾਦ ਦੋਵੇਂ ਸਪਲਾਈ ਕਰਦੇ ਹਾਂ
2. ਨਿਰਮਾਤਾ ਤੋਂ ਸਿੱਧੇ ਗਾਹਕ ਤੱਕ, ਤੁਹਾਡੀ ਲਾਗਤ ਨੂੰ ਬਚਾਓ
3. ਆਮ ਹਿੱਸੇ ਲਈ ਸਥਿਰ ਸਟਾਕ
4. ਸਮੇਂ ਦੀ ਡਿਲਿਵਰੀ ਸਮੇਂ ਵਿੱਚ, ਪ੍ਰਤੀਯੋਗੀ ਸ਼ਿਪਿੰਗ ਲਾਗਤ ਦੇ ਨਾਲ
5. ਪੇਸ਼ੇਵਰ ਅਤੇ ਸੇਵਾ ਦੇ ਬਾਅਦ ਸਮੇਂ 'ਤੇ
ਪੈਕਿੰਗ
ਗੱਤੇ ਦੇ ਬਕਸੇ, ਜਾਂ ਗਾਹਕਾਂ ਦੀ ਬੇਨਤੀ ਦੇ ਅਨੁਸਾਰ.
ਬਾਲਟੀ ਸਿਲੰਡਰ ਦੇ ਨੁਕਸਾਨ ਦੇ ਕਾਰਨ ਅਤੇ ਰੱਖ-ਰਖਾਅ
ਜਦੋਂ ਇੱਕ ਹਾਈਡ੍ਰੌਲਿਕ ਖੁਦਾਈ ਕਰਨ ਵਾਲਾ ਖੋਦਣ ਦਾ ਕੰਮ ਕਰ ਰਿਹਾ ਸੀ, ਤਾਂ ਬਾਲਟੀ ਦੀ ਗਤੀ ਹੌਲੀ-ਹੌਲੀ ਹੌਲੀ ਹੋ ਜਾਂਦੀ ਹੈ ਜਦੋਂ ਤੱਕ ਇਹ ਆਮ ਤੌਰ 'ਤੇ ਕੰਮ ਨਹੀਂ ਕਰ ਸਕਦਾ ਸੀ। ਵਿਸ਼ਲੇਸ਼ਣ ਦਾ ਮੰਨਣਾ ਹੈ ਕਿ ਬਾਲਟੀ ਸਿਲੰਡਰ ਖਰਾਬ ਹੋ ਸਕਦਾ ਹੈ।
1. ਨਿਰੀਖਣ ਦੇ ਤਰੀਕੇ ਅਤੇ ਨਤੀਜੇ
ਜਦੋਂ ਬਾਲਟੀ ਸਿਲੰਡਰ ਹੌਲੀ-ਹੌਲੀ ਚਲਦਾ ਹੈ ਜਾਂ ਹਿੱਲਦਾ ਨਹੀਂ ਹੈ, ਤਾਂ ਪਹਿਲਾਂ ਇਸਦੀ ਦਿੱਖ ਦੀ ਜਾਂਚ ਕਰੋ, ਅਤੇ ਜੇਕਰ ਕੋਈ ਅਸਧਾਰਨਤਾ ਨਹੀਂ ਹੈ, ਤਾਂ ਤੇਲ ਰਿਟਰਨ ਫਿਲਟਰ ਤੱਤਾਂ ਦੀ ਜਾਂਚ ਕਰੋ।
ਬਾਲਟੀ ਸਿਲੰਡਰ ਪਿਸਟਨ ਦੇ ਬਹੁਤ ਜ਼ਿਆਦਾ ਕੰਮ ਦੇ ਨਾਲ, ਪਹਿਨਣ ਅਤੇ ਹੋਰ ਕਾਰਨਾਂ ਕਰਕੇ ਪੈਦਾ ਹੋਏ ਕਣ ਵਹਿਣ ਲਈ ਕਾਰਜਸ਼ੀਲ ਮਾਧਿਅਮ ਵਿੱਚ ਬਦਲ ਜਾਣਗੇ, ਅਤੇ ਤੇਲ ਰਿਟਰਨ ਪਾਈਪਲਾਈਨ ਵਿੱਚ ਤੇਲ ਰਿਟਰਨ ਫਿਲਟਰ ਤੱਤ ਦੁਆਰਾ ਰੋਕਿਆ ਜਾਵੇਗਾ। ਜੇ ਤੇਲ ਰਿਟਰਨ ਫਿਲਟਰ ਤੱਤ ਵਿੱਚ ਇੱਕ ਕਾਲਾ ਰਬੜ ਬਲਾਕ ਪ੍ਰਵੇਸ਼ ਕਰਦਾ ਹੈ, ਤਾਂ ਪਿਸਟਨ ਸੀਲ ਰਿੰਗ ਸਪੱਸ਼ਟ ਤੌਰ 'ਤੇ ਨੁਕਸਾਨੀ ਜਾਂਦੀ ਹੈ; ਜੇਕਰ ਵੱਖ-ਵੱਖ ਆਕਾਰਾਂ ਦੀਆਂ ਲੋਹੇ ਦੀਆਂ ਫਾਈਲਾਂ ਮਿਲਦੀਆਂ ਹਨ, ਤਾਂ ਇਹ ਦਰਸਾਉਂਦਾ ਹੈ ਕਿ ਸਟੀਲ ਸੀਲ ਰਿੰਗ ਅਤੇ ਸਿਲੰਡਰ ਦੀ ਅੰਦਰਲੀ ਕੰਧ ਵਿਚਕਾਰ ਰਗੜ ਕਾਰਨ ਕਣ ਪੈਦਾ ਹੁੰਦੇ ਹਨ; ਜੇਕਰ ਸਲੇਟੀ ਜਾਂ ਹਲਕਾ ਪੀਲਾ ਅੱਧਾ ਪਾਰਦਰਸ਼ੀ ਨਾਈਲੋਨ ਸਮੱਗਰੀ ਹੈ ਤਾਂ ਪਹਿਨਣ ਵਾਲੀ ਰਿੰਗ ਦੇ ਨੁਕਸਾਨ ਨੂੰ ਦਰਸਾਉਂਦੀ ਹੈ।
ਜਾਂਚ ਤੋਂ ਬਾਅਦ ਪਾਇਆ ਗਿਆ ਕਿ ਮਸ਼ੀਨ ਦੇ ਆਇਲ ਰਿਟਰਨ ਫਿਲਟਰ ਐਲੀਮੈਂਟ ਵਿੱਚ ਵੱਡੀ ਮਾਤਰਾ ਵਿੱਚ ਮੈਟਲ ਪਾਊਡਰ, ਬਲੈਕ ਰਬੜ ਬਲਾਕ, ਭੂਰਾ ਨਾਈਲੋਨ ਅਤੇ ਛੋਟੇ ਧਾਤ ਦੇ ਕਣ ਸਨ। ਰਿੰਗ ਪਿਸਟਨ ਰਿੰਗ ਗਰੂਵ ਵਿੱਚ ਫਸ ਗਈ ਹੈ ਅਤੇ ਟੁੱਟ ਗਈ ਹੈ। ਸਿਲੰਡਰ ਦੀ ਅੰਦਰਲੀ ਕੰਧ ਬੁਰੀ ਤਰ੍ਹਾਂ ਨਾਲ ਖਿਸਕ ਗਈ ਹੈ। ਸਿਲੰਡਰ ਦੇ ਹੇਠਾਂ ਬਹੁਤ ਸਾਰੇ ਮੈਟਲ ਪਾਊਡਰ ਅਤੇ ਕਣ ਹਨ.
2. ਕਾਰਨ ਵਿਸ਼ਲੇਸ਼ਣ
ਵਿਸ਼ਲੇਸ਼ਣ ਦਾ ਮੰਨਣਾ ਹੈ ਕਿ ਧਾਤ ਦੀ ਥਕਾਵਟ ਵਰਗੇ ਕਾਰਕਾਂ ਕਾਰਨ, ਬਾਲਟੀ ਸਿਲੰਡਰ ਪਿਸਟਨ 'ਤੇ ਸਟੀਲ ਦੀ ਰਿੰਗ ਟੁੱਟ ਜਾਂਦੀ ਹੈ, ਜਿਸ ਨਾਲ ਪਿਸਟਨ ਅਤੇ ਸਿਲੰਡਰ ਵਿਚਕਾਰ ਸਿੱਧਾ ਸੰਪਰਕ ਹੁੰਦਾ ਹੈ। ਪਿਸਟਨ ਰਾਡ ਦੇ ਲਗਾਤਾਰ ਫੈਲਣ ਅਤੇ ਸੁੰਗੜਨ ਦੇ ਦੌਰਾਨ, ਸਟੀਲ ਰਿੰਗ ਦਾ ਸਟਬਲ ਬਾਲਟੀ ਸਿਲੰਡਰ ਦੀ ਅੰਦਰਲੀ ਕੰਧ ਨੂੰ ਖੁਰਚਣਾ ਜਾਰੀ ਰੱਖਦਾ ਹੈ। ਕੰਧ ਅੰਦਰੂਨੀ ਲੀਕੇਜ ਦਾ ਕਾਰਨ ਬਣ ਜਾਂਦੀ ਹੈ, ਜੋ ਬਾਲਟੀ ਸਿਲੰਡਰ ਦੀ ਗਤੀ ਨੂੰ ਘਟਾਉਂਦੀ ਹੈ। ਕੰਮ ਦੇ ਘੰਟੇ ਵਧਣ ਨਾਲ, ਸੀਲ ਰਿੰਗ ਦਾ ਨੁਕਸਾਨ ਅਤੇ ਸਿਲੰਡਰ ਦੀ ਕੰਧ 'ਤੇ ਦਬਾਅ ਵਧਦਾ ਜਾ ਰਿਹਾ ਹੈ, ਜਿਸ ਨਾਲ ਬਾਲਟੀ ਸਿਲੰਡਰ ਦੀ ਅੰਦਰੂਨੀ ਲੀਕੇਜ ਹੋਰ ਗੰਭੀਰ ਹੋ ਜਾਂਦੀ ਹੈ, ਜਿਸ ਨਾਲ ਕੰਟਰੋਲ ਵਾਲਵ ਬਾਲਟੀ ਸਿਲੰਡਰ ਦੀ ਕਾਰਵਾਈ ਨੂੰ ਨਿਯੰਤਰਿਤ ਨਹੀਂ ਕਰ ਸਕਦਾ ਹੈ। .
3. ਰੋਕਥਾਮ ਉਪਾਅ
(1) ਮਿਆਰੀ ਕਾਰਵਾਈ
ਖੁਦਾਈ ਦੀ ਕਾਰਵਾਈ ਵਿੱਚ, ਜੇਕਰ ਬਾਲਟੀ ਸਿਲੰਡਰ ਪਿਸਟਨ ਰਾਡ ਰਾਡ ਕੈਵਿਟੀ ਸਟ੍ਰੋਕ ਦੇ ਅੰਤ ਤੱਕ ਪਹੁੰਚ ਜਾਂਦੀ ਹੈ, ਤਾਂ ਅੰਦਰੂਨੀ ਸੀਮਾ ਰਿੰਗ ਦਬਾਅ ਅਤੇ ਪ੍ਰਭਾਵ ਦੀ ਕਿਰਿਆ ਦੇ ਅਧੀਨ ਆਸਾਨੀ ਨਾਲ ਨੁਕਸਾਨੇ ਜਾਏਗੀ, ਜਿਸ ਨਾਲ ਬਾਲਟੀ ਸਿਲੰਡਰ ਦੀ ਸੇਵਾ ਜੀਵਨ ਨੂੰ ਘਟਾ ਦਿੱਤਾ ਜਾਵੇਗਾ। ਇਸ ਲਈ, ਮਸ਼ੀਨ ਨੂੰ ਚਲਾਉਂਦੇ ਸਮੇਂ, ਬਾਲਟੀ ਸਿਲੰਡਰ ਨੂੰ 10-20 ਸੈਂਟੀਮੀਟਰ ਦਾ ਵਿਸਤਾਰ ਅਤੇ ਸੰਕੁਚਨ ਭੱਤਾ ਬਰਕਰਾਰ ਰੱਖਣਾ ਚਾਹੀਦਾ ਹੈ। ਇਹ ਓਪਰੇਸ਼ਨ ਲੰਬੇ ਸਮੇਂ ਦੇ ਭਾਰੀ ਲੋਡ ਪ੍ਰਭਾਵ ਦੇ ਕਾਰਨ ਸਟੀਲ ਰਿੰਗ ਨੂੰ ਥਕਾਵਟ ਦੇ ਨੁਕਸਾਨ ਨੂੰ ਰੋਕ ਸਕਦਾ ਹੈ ਅਤੇ ਪਿਸਟਨ 'ਤੇ ਰਿੰਗ ਨੂੰ ਸੀਮਤ ਕਰ ਸਕਦਾ ਹੈ।
ਜਦੋਂ ਖੁਦਾਈ ਕਰਨ ਵਾਲਾ ਕੰਮ ਕਰ ਰਿਹਾ ਹੈ, ਤਾਂ ਖੁਦਾਈ ਦੀ ਡੂੰਘਾਈ ਅਤੇ ਖੁਦਾਈ ਦੀ ਰੇਂਜ ਲਗਾਤਾਰ ਬਦਲ ਰਹੀ ਹੈ। ਇਸ ਲਈ, ਬਾਲਟੀ ਸਿਲੰਡਰ ਅਤੇ ਕਨੈਕਟਿੰਗ ਰਾਡ, ਸਟਿਕ ਸਿਲੰਡਰ ਅਤੇ ਸੋਟੀ ਨੂੰ ਓਪਰੇਸ਼ਨ ਦੌਰਾਨ ਜਿੰਨਾ ਸੰਭਵ ਹੋ ਸਕੇ 90° 'ਤੇ ਕੋਣ ਕੀਤਾ ਜਾਣਾ ਚਾਹੀਦਾ ਹੈ, ਅਤੇ ਇਸਨੂੰ ਹਮੇਸ਼ਾ ਸਟਰੋਕ ਦੇ ਅੰਤ ਤੱਕ ਨਾ ਪਹੁੰਚਾਓ। ਇਸ ਤਰ੍ਹਾਂ, ਖੁਦਾਈ ਕਰਨ ਵਾਲਾ ਵੱਧ ਤੋਂ ਵੱਧ ਖੁਦਾਈ ਸ਼ਕਤੀ ਅਤੇ ਵੱਧ ਤੋਂ ਵੱਧ ਕਾਰਜ ਕੁਸ਼ਲਤਾ ਪ੍ਰਾਪਤ ਕਰ ਸਕਦਾ ਹੈ।
(2) ਵਾਜਬ ਰੱਖ-ਰਖਾਅ
ਖੁਦਾਈ ਕਰਨ ਵਾਲੇ ਦੀਆਂ ਓਪਰੇਟਿੰਗ ਆਈਟਮਾਂ ਅਤੇ ਓਪਰੇਟਿੰਗ ਹਾਲਤਾਂ ਦੇ ਅਨੁਸਾਰ, ਵਾਜਬ ਤੇਲ ਦੀ ਤਬਦੀਲੀ ਅਤੇ ਰੱਖ-ਰਖਾਅ ਸਥਾਨਕ ਸਥਿਤੀਆਂ ਦੇ ਅਨੁਸਾਰ ਕੀਤੀ ਜਾਣੀ ਚਾਹੀਦੀ ਹੈ.
ਸਾਡਾ-ਗੁਦਾਮ ।੧।ਰਹਾਉ
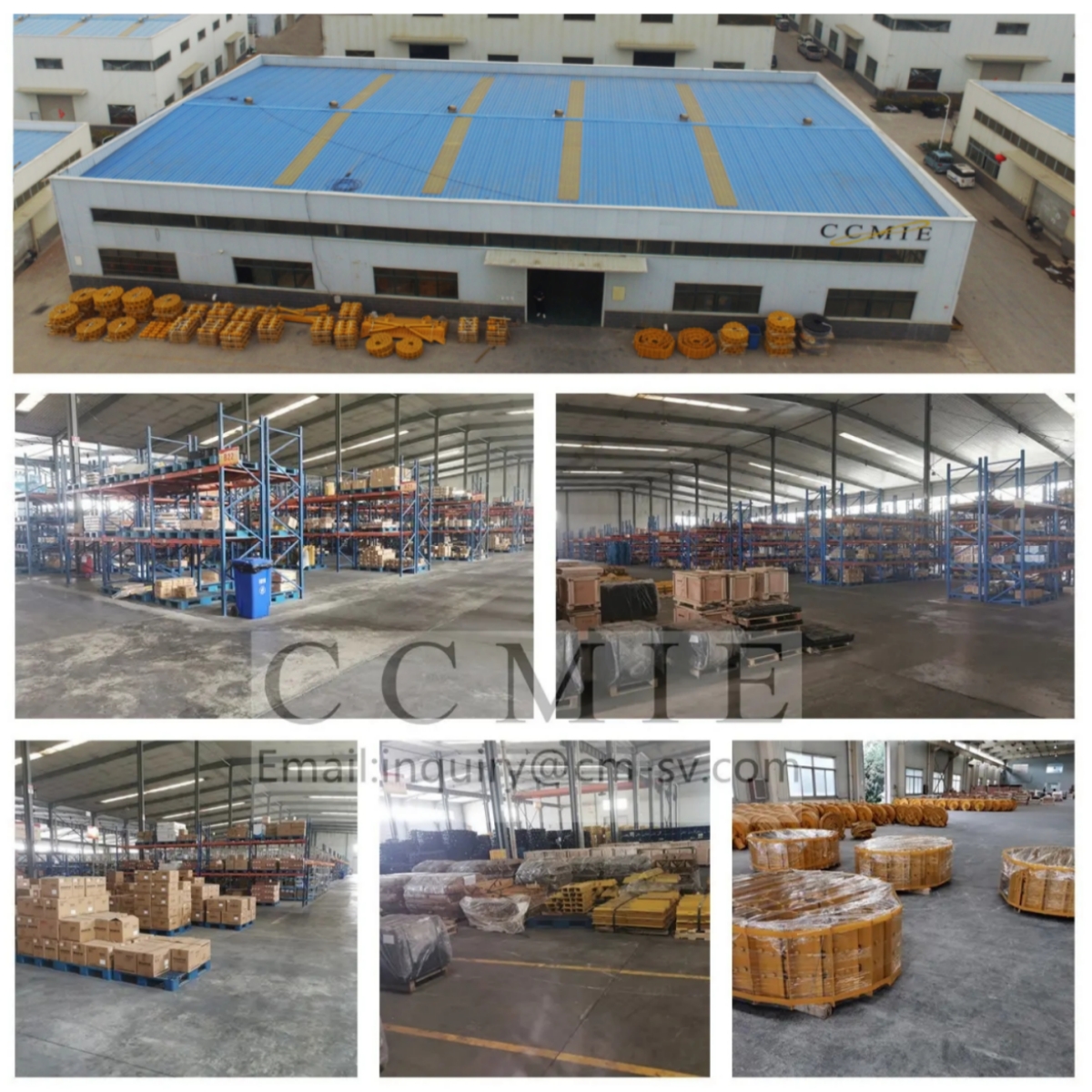
ਪੈਕ ਅਤੇ ਜਹਾਜ਼

- ਏਰੀਅਲ ਬੂਮ ਲਿਫਟ
- ਚੀਨ ਡੰਪ ਟਰੱਕ
- ਕੋਲਡ ਰੀਸਾਈਕਲਰ
- ਕੋਨ ਕਰੱਸ਼ਰ ਲਾਈਨਰ
- ਕੰਟੇਨਰ ਸਾਈਡ ਲਿਫਟਰ
- ਦਾਦੀ ਬੁਲਡੋਜ਼ਰ ਭਾਗ
- ਫੋਰਕਲਿਫਟ ਸਵੀਪਰ ਅਟੈਚਮੈਂਟ
- Hbxg ਬੁਲਡੋਜ਼ਰ ਪਾਰਟਸ
- ਹੋਵੋ ਇੰਜਣ ਦੇ ਹਿੱਸੇ
- ਹੁੰਡਈ ਖੁਦਾਈ ਹਾਈਡ੍ਰੌਲਿਕ ਪੰਪ
- Komatsu ਬੁਲਡੋਜ਼ਰ ਦੇ ਹਿੱਸੇ
- Komatsu ਖੁਦਾਈ ਗੇਅਰ ਸ਼ਾਫਟ
- Komatsu Pc300-7 ਖੁਦਾਈ ਹਾਈਡ੍ਰੌਲਿਕ ਪੰਪ
- ਲਿਓਗੋਂਗ ਬੁਲਡੋਜ਼ਰ ਦੇ ਹਿੱਸੇ
- ਸੈਨੀ ਕੰਕਰੀਟ ਪੰਪ ਸਪੇਅਰ ਪਾਰਟਸ
- ਸੈਨੀ ਐਕਸੈਵੇਟਰ ਸਪੇਅਰ ਪਾਰਟਸ
- ਸ਼ੈਕਮੈਨ ਇੰਜਣ ਦੇ ਹਿੱਸੇ
- ਸ਼ਾਂਤੁਈ ਬੁਲਡੋਜ਼ਰ ਕਲਚ ਸ਼ਾਫਟ
- ਸ਼ਾਂਤੁਈ ਬੁਲਡੋਜ਼ਰ ਕਨੈਕਟਿੰਗ ਸ਼ਾਫਟ ਪਿੰਨ
- Shantui ਬੁਲਡੋਜ਼ਰ ਕੰਟਰੋਲ ਲਚਕਦਾਰ ਸ਼ਾਫਟ
- ਸ਼ਾਂਤੁਈ ਬੁਲਡੋਜ਼ਰ ਲਚਕਦਾਰ ਸ਼ਾਫਟ
- ਸ਼ਾਂਤੂਈ ਬੁਲਡੋਜ਼ਰ ਲਿਫਟਿੰਗ ਸਿਲੰਡਰ ਮੁਰੰਮਤ ਕਿੱਟ
- ਸ਼ਾਂਤੁਈ ਬੁਲਡੋਜ਼ਰ ਦੇ ਹਿੱਸੇ
- ਸ਼ਾਂਤੁਈ ਬੁਲਡੋਜ਼ਰ ਰੀਲ ਸ਼ਾਫਟ
- ਸ਼ਾਂਤੁਈ ਬੁਲਡੋਜ਼ਰ ਰਿਵਰਸ ਗੇਅਰ ਸ਼ਾਫਟ
- Shantui ਬੁਲਡੋਜ਼ਰ ਸਪੇਅਰ ਪਾਰਟਸ
- ਸ਼ਾਂਤੁਈ ਬੁਲਡੋਜ਼ਰ ਵਿੰਚ ਡਰਾਈਵ ਸ਼ਾਫਟ
- ਸ਼ਾਂਤੁਈ ਡੋਜ਼ਰ ਬੋਲਟ
- ਸ਼ਾਂਤੂਈ ਡੋਜ਼ਰ ਫਰੰਟ ਆਈਡਲਰ
- ਸ਼ਾਂਤੂਈ ਡੋਜ਼ਰ ਟਿਲਟ ਸਿਲੰਡਰ ਮੁਰੰਮਤ ਕਿੱਟ
- Shantui Sd16 ਬੇਵਲ ਗੇਅਰ
- Shantui Sd16 ਬ੍ਰੇਕ ਲਾਈਨਿੰਗ
- Shantui Sd16 ਡੋਰ ਅਸੈਂਬਲੀ
- Shantui Sd16 O-ਰਿੰਗ
- Shantui Sd16 ਟਰੈਕ ਰੋਲਰ
- Shantui Sd22 ਬੇਅਰਿੰਗ ਸਲੀਵ
- Shantui Sd22 ਫਰੀਕਸ਼ਨ ਡਿਸਕ
- Shantui Sd32 ਟਰੈਕ ਰੋਲਰ
- Sinotruk ਇੰਜਣ ਦੇ ਹਿੱਸੇ
- ਟੋਅ ਟਰੱਕ
- Xcmg ਬੁਲਡੋਜ਼ਰ ਦੇ ਹਿੱਸੇ
- Xcmg ਬੁਲਡੋਜ਼ਰ ਸਪੇਅਰ ਪਾਰਟਸ
- Xcmg ਹਾਈਡ੍ਰੌਲਿਕ ਲਾਕ
- Xcmg ਟ੍ਰਾਂਸਮਿਸ਼ਨ
- Yuchai ਇੰਜਣ ਦੇ ਹਿੱਸੇ